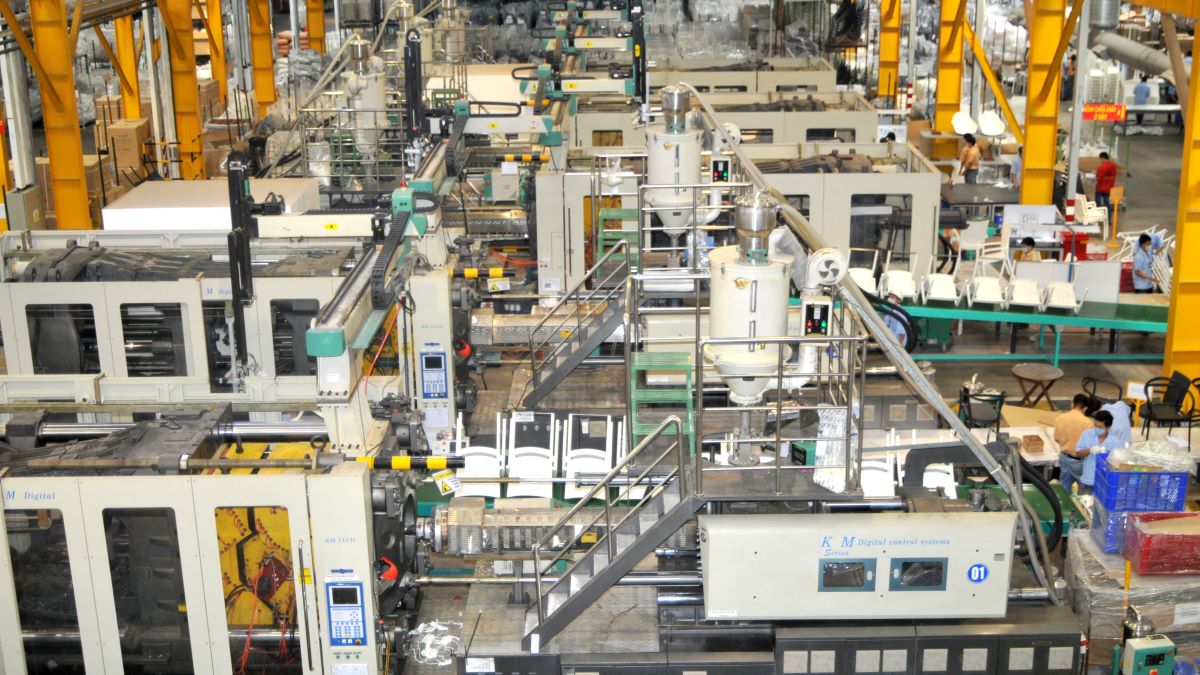
ScanCom is a leading global manufacturer of premium quality outdoor furniture with headquarters in Denmark and its main production facilities located in Ho Chi Minh City, Vietnam. Since being founded in 1995 ScanCom has grown to become a highly respected, ethical manufacturer with a proven commitment to CSR and the company prides itself on “Doing Business the Right Way”, the corporate motto. Although the company employs over 5,000 people worldwide, in recent years advanced technology and ScanCom’s long term vision have combined to drive a definite shift towards increased automation in the company’s production facilities. I met with ScanCom’s Commercial Director, Dutchman Rene De Kok, to discuss some of the issues surrounding adoption of automated technology.
“With labour costs rapidly rising across Asia, manufacturers are facing the same challenges that their counterparts in Europe and North America faced around fifty years ago. As a result of this shift, automation is going to become increasingly important for the industry and at ScanCom we have ensured that we have continued to incorporate state-of-the-art technology into our production processes.” Such developments have led to two major improvements according to Mr De Kok: the ability to increase productivity in the manufacturing facilities and a higher quality end product.
The drive to embrace technological advancement has seen ScanCom significantly increase and improve its robot manufacturing capabilities, a process which started in 2010 with the focus on wood production. As Mr. De Kok explains: “There was a significant investment of capital into automation at that time with the major aims being an increase in the speed at which our wooden products could be made and an improvement in the quality of the final piece.” The project turned out to be highly successful and the initiative of increased automation was rolled out to all of the company’s production facilities. For example, in terms of aluminium production, hand-welding had been the traditional method whereas now, since the introduction of the first robotic welding machine in 2014, between 40 and 50 per cent of ScanCom’s aluminium production is now fully automated.
As Mr De Kok explains though, automation poses its own challenges, in the short-term at least: “Learning how to get the most of the machinery, mastering the technology, is a process and doesn’t happen overnight. In our case, we have become increasingly adept with the technology, particularly in terms of correctly calibrating the equipment, and when the machinery is at an optimum level of operation the increases in productivity and quality can be enormous. It must also be said that members of the workforce have made a significant contribution to the process of mastering the technology and helping ScanCom reap the rewards of increased automation. “Numerous engineers within our workforce have added to the increased understanding and awareness of how the technology might be best utilized and the value of such knowledge and expertise cannot be underestimated.”
Additionally, the cost of employing human beings is actually lower than operating robots, a fact that many outside the industry are unaware of. From ScanCom’s point of view, the cost of the technology and investment in automation represents a considerable outlay that needs to be recouped, and it is for this reason that the robotic welders work three shifts a day. In De Kok’s words: “In terms of cost, in this case the difference between robots and humans is minimal but the real value lies in the significantly improved output and quality of the final product. There is no doubt that automation is going to become an increasingly visible trend within the industry and ScanCom is in the ideal position to capitalize on that shift.”
As a manufacturer in Vietnam, ScanCom’s strategy of investment in technology in order to optimize efficiency makes the company unique among its competitors in the country. The cost of state-of-the-art machinery is high, with one Bacci CNC (computer numerical control) machine costing approximately $300, 000. The scale of investment is simply too large for most manufacturers who do not see the value in the current market climate and many of these organisations simply add more people to the work force. ScanCom, as De Kok illustrates, is looking further ahead than most in the industry: “As a company, we cannot see how increasing the workforce is a viable solution to the longer term challenges facing the industry and that is one of the key factors in our strategic decision to proactively implement these improvements in order to safeguard longer term competitiveness.”
Recent acquisitions of automated equipment have been noteworthy: 7 welding robots to be shared between ScanCom’s aluminium and steel production facilities, and 2 Opticut machines and a further 10 CNC machines have been installed in the wood production facility helping to improve the speed and accuracy of the process. This highly sophisticated equipment has gone hand in hand with ScanCom’s desire to continuously innovate and obtain optimum output, as it also allows maximum utilization of raw materials. With a material like aluminium being relatively expensive, the advantages are clear.
Another tangible illustration of ScanCom’s desire to ongoing expansion and growth is the decision, taken just under 2 years ago, to move into plastics manufacturing using cutting-edge technology and equipment. 9 injection molding machines - 8 of which are gas assisted - have been installed in ScanCom’s production facilities in Vietnam and De Kok gives some further insights into this strategic decision: “Like many industries, outdoor furniture is cyclical and in recent years it has become clear that plastics manufacturing has really come back to the fore. Although that area of production needs a lot of automation due to injection molding, a great deal of manual labour is also required to facilitate the production so it makes sense to undertake the activity in Asia.”
ScanCom is recognized for the ability to make products that combine materials in new and interesting ways and De Kok believes the expansion into plastics has only served to enhance that perception: “Investing in state-of-the-art technology and applying expertise to plastics has allowed us to produce even more innovative and unique products due to the range of materials that is at our disposal. Duresin®, which is the brand name we give to our plastic formulations, has allowed greater scope in terms of design and innovation and this has been demonstrated by the growth in that area of our business in the last 18 months.”
It is not only technology that ScanCom aims to continuously improve and invest in; CSR and the safety and wellbeing of its employees are also fundamentals upon which the company motto of “Doing Business the Right Way” is built. “It is an area we take very seriously indeed and our emphasis on best practices is in evidence throughout all areas of the business”, says De Kok. A prestigious CSR award, recently given by the Danish ministry, demonstrates this and ScanCom receives a great deal of recognition for being leaders in the industry in terms of the benchmarks set for safety, quality and sustainability with their operations often being cited as exemplary.
With such a focus on improvement and development in these areas, ScanCom is set to reap the benefits of the recently agreed Trans-Pacific Partnership (TPP), a trade agreement between 12 Pacific Rim nations that seeks to promote economic growth and improvement in all aspects of trade. Although the agreement has yet to be finalized and the effects of it are still relatively uncertain, De Kok feels that ScanCom’s production base in Vietnam will be positively affected by it and views the company’s aim of being at the forefront of automation and CSR as key factors in the future success of the group: “We are optimistic that it will serve to enhance the attractiveness of Vietnam as a location for manufacturing and will allow ScanCom further opportunities to continue to demonstrate its leadership within the outdoor furniture industry.”